So you want to setup some outdoor Christmas LED lights around your home and garden, and you tried solar for a while, but realized they really aren’t very powerful, and don’t last very long, so you figured you need to use “low voltage” lights.
Low voltage lights have a mini power adapter and a long cable that connects to the lights. While you can run mains power out to your garden and put you adapter in a waterproof container, the best solution is to have the adapter inside and connect it to the lights outside. The question is how to do that.
In my case I have run cat5 network cables from the patch panel area inside the house, to a watertight junction box outside. I have also purchased a spare set of low voltage lights, on special for $5, and I will cannibalize them to create a socket and plug set.
The plug cable, the bit inside the house, can be made easily by cutting the plug off the end of the light set. The socket end, which will go outside, is much harder. This post describes how to take the light sets power adapter and turn it a sturdy watertight socket that can be left outside and connected to my cat5 cable.

Creating the socket cable
For those of you who want the quick answer I have created a video with the full process. Details about precisely what I used are described further down on this page along with a text version of the process
The YouTube video version
The text version
The tools and parts you need are described in more detail below. These should serve as ideas on how to create the socket, more than likely your situation will vary and you will need to work out what works for you – hopefully this guide can give you some inspiration. As such don’t feel you should hunt down exactly the same items as me!
Despite this being the text version of the process, I would still strongly suggest you watch the video as the two complement each other.
Cut the socket from the power adapter
For the type of power adapter we are using, the socket part is built into the adapter casing and it just plugs into the main board

I start by putting a spacer around the thread of the socket and then use a hole saw to drill around the socket. This means the socket just pulls out. Thus the steps are:
- Put a spacer, buteline in my case, around the thread of the socket so that you cut evenly around the socket, and don’t cut too close to the thread. You may have to hunt around a bit to find a spacer and hole saw that all align size wise.
- Put this in a vice, put a hole saw on your drill and then put the hole saw over the spacer/buteline
- Drill out the socket
- Voilà it’s done, just pull out the socket and clean it up

Create the shell for the socket
As I mentioned earlier, this post should serve to give you ideas on how to do things, you don’t necessarily need to use the same parts as me or create the socket exactly the same way. For me the shell of the socket is a 20mm conduit joiner, the type of thing you would use to join to pieces of 20mm conduit.
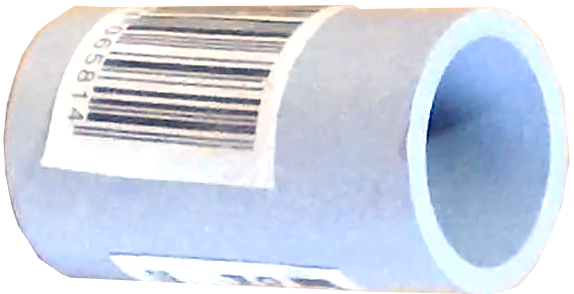
Apart from the physical dimensions of the joiner being right, the other thing that makes it useful is that it has a ridge on the inside. Thus if you were to slice a joiner from one end to the other it would look like:

Then we can take the socket, that we drilled out of the power adapter, and when we slide it into the joiner it would rest on the ridge like so:

The first thing we need to do is to cut the joiner just next to one side of the ridge on the joiner and then file it down so the ridge part is reasonably small. First thing is to mark the joiner so we know where to cut. Do this using the conduit we cut in half as a guide. Then put it in the vice and cut it:

After filing and sanding it down it looks like:

Before we can slide the socket into the modified joiner we need to gradually file down the edge of the socket so it is a snug fit. To do this we just gradually file around the side of the socket and keep trying to fit it into the joiner. This is a bit tedious, but it will give us the important tight fit we need.

It is also worth noting that the joiner does narrow slightly towards the center, just where we cut it in half. So you will notice it fits at the end but then gets tighter the further you push the socket into the joiner
Assemble the socket
Step one is to solder the wire to the socket:

Next push the socket into the joiner. After that add a spacer/washer type of thing and finally put the plug into it and screw it all up. When you are finished it should look like:

Put the silicone at the back
The final step in creating the socket is to add silicone at the back to both seal the connection between the wire and the socket, and also to “glue” the socket into the conduit joiner. I usually do this in two steps, applying half the silicone each time, with a few days between, because I think that means it will cure better – but I am no expert.
Also you might find there are other things which are better than silicone, like for example builders bog. I haven’t really done a lot of experimenting as silicone seems to work fine.
Be careful to keep the wire, at the back of the socket, nice and straight so it cures that way.

All finished!

Tools
Drill
Drill – This can be cordless, wired and probably even a hand drill
Saw
We only use this for cutting the conduit, I have used a hack saw but any saw will probably do
Soldering iron
Nothing special here, we just have a couple of wires to solder to the socket. Any soldering iron and solder should probably do.
Vice
We need to cut and file down the both conduit joiner and power adapter socket. An average metal vice is probably best.
Hole saw
For my scenario I used a 25mm long hole saw. My thinking was that the longer hole saw was better because you had to be able to fit the socket into the hole saw, but on reflection that doesn’t seem to be so much of a problem as you can see from the below photo with the longer hole saw vs the standard one.

Parts
Silicon sealant
I used Gorilla “Plumbers” silicone sealant. I wanted something that would make the back of the socket waterproof and be able to withstand the outside conditions.
Christmas light set

All we really want is the power adapter and plug, we don’t use the lights. I just get the cheap ones after Christmas, the light sets that aren’t popular, usually I can get them for $5 or so
20mm conduit joiner
I needed to find something I could use to hold the socket side of the light cord. It needed to be a tight fit and the conduit joiner did the trick. There are bound to be lots of other things you could use but this is what I used. It is a Bunnings “Deta 20mm Grey Conduit Fittings Plain Coupling.
Worth noting that along with the ridge that is half way inside the joiner, you should not that the inside of the joiner gets progressively narrower as you get to the center, presumably to grip the conduit pipe.
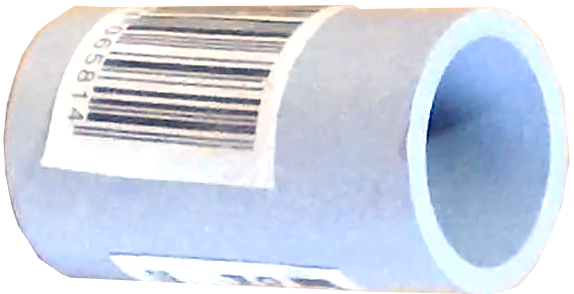
Wire
Obviously this will vary quite a bit depending on your requirements. The wire used in the led themselves is typically extremely thin, presumably to save costs. Given the amount of effort you are putting into this exercise it makes sense to have something thicker, most likely this will depend on what you have at hand or what you can get for a good price.

Large spacer/washer
When we assemble everything together, the socket, the conduit joiner, wire and silicone, we need a spacer which is about 2mm thick and with a hole only just big enough to fit the socket through it. For me the simple solution was a thin piece of wood with a hole drilled in it. Yes it’s not particularly pretty, but it’s easy to get, it’s exactly the right dimensions, it works well, and most of all it’s only used during the build process, so who cares what it looks like:
This is what my one looks like:
